Tomi Pitkäaho
Athith Sagar
Tero Kaarlela
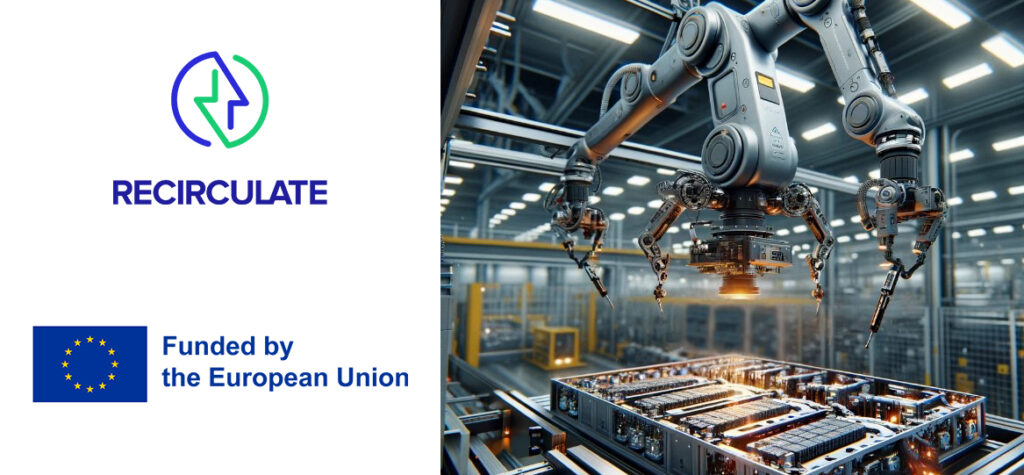
The rapid growth in battery demand raises questions about sustainability and the limited amount of rare materials. While recycling the batteries to raw materials enables the preservation of rare raw materials, recycling consumes time and energy, reducing the value of recycled batteries. Repurposing and reusing for second-life applications is resource-wise compared to recycling.
The RECIRCULATE project includes concepts for reusing, recycling, robotic dismantling and sorting of batteries to increase sustainability, safety, and cost-effectiveness. An online kick-off meeting to start the RECIRCULATE project was held in June 2023. The project’s budget is about six million Euros, and it comprises a network of 11 partners from eight European countries. In addition to coordinating the project, Centria is leading a work package focusing on developing a robotized solution for EV battery dismantling and sorting.
Partners and work packages
Coordinating a Horizon project is a new experience for Centria and enables us to gain experience leading a large EU Horizon project consortium. In addition to coordination, Centria is responsible for developing solutions for robotized dismantling of battery packs. The RECIRCULATE project is divided into six work packages consisting of tasks, deliverables, and milestones. Each work package has a leading organization ensuring the tasks will progress according to the agreement. The other members of the work package support the leading organization. Figure 1 presents the RECIRCULATE concept for processing the batteries.
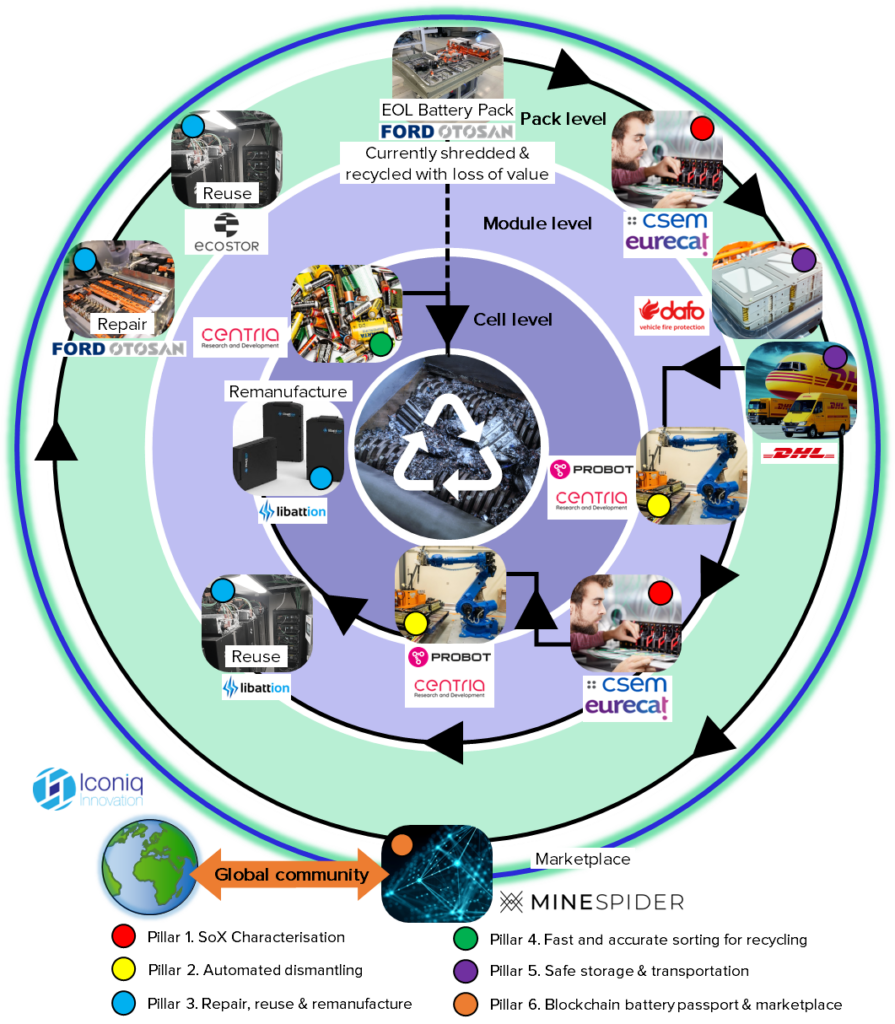
CSEM (Swiss Center for Electronics and Microtechnology, Switzerland) leads the first work package. The goal is assessment, evaluation, and safe transportation of batteries. In this work package, CSEM will develop methods for fast, cost-effective and reliable characterization of the battery pack before transporting EV batteries to the dismantling and sorting facility. Centria, in addition to coordinating the project, is responsible for the second work package. The work package led by Centria aims to develop the concept and methods for the automated dismantling of batteries. The batteries are dismantled from complete packs to modules and, if needed, from modules to cells. Probot (Probot OY, Finland) is responsible for the demonstration in an industrially relevant environment. The plan is to implement the industrial dismantling and sorting cell into a freight container to enable an isolated mobile solution. Relocation of the containerized dismantling system enables easy establishment at the production premises and fast isolation in case of fire. Minespider (Minespider Germany GmbH) leads the third work package, focusing on developing a blockchain-based battery passport to track the battery data. Battery passport enables a circular economy system for EV batteries and is the base for a unique, blockchain-based virtual EV battery marketplace. ECO STOR (ECO STOR AS, Norway) and Libattion (Libattion AG, Switzerland)focus on second-life applications, recycling, and sustainability of the EV battery packs in the fourth work package. Repurposed EV battery packs are marketed as residential, commercial, and industrial energy storage and provide online monitoring systems. An example of 2nd life application of building energy storage product built reusing Ford plug-in-hybrid battery packs is shown in Figure 2.
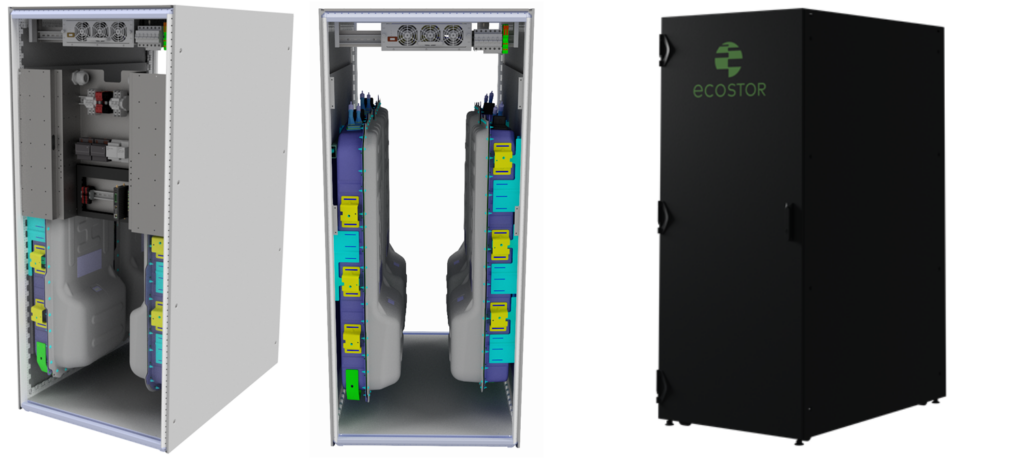
The fifth work package community building is led by Minespider and supported by all the consortium members. Effective dissemination is essential to the project’s success; no matter how good the concepts and methods we develop, it is useless if no one knows about our work. The sixth work package is the project administration, led by Centria in collaboration with Iconiq Innovation. The tasks of this work package ensure efficient communication with the European Commission, within the consortium, and with the external advisory board to reach a common understanding between different parties. Figure 3. presents the locations of the project partners. In addition to supplying batteries FORD Otosan and Eurecat (Fundacio Eurecat, Spain) are preparing an environmental impact study and conduct a Cradle-to-Grave Life Cycle Assessment (LCA) of the batteries in the project.
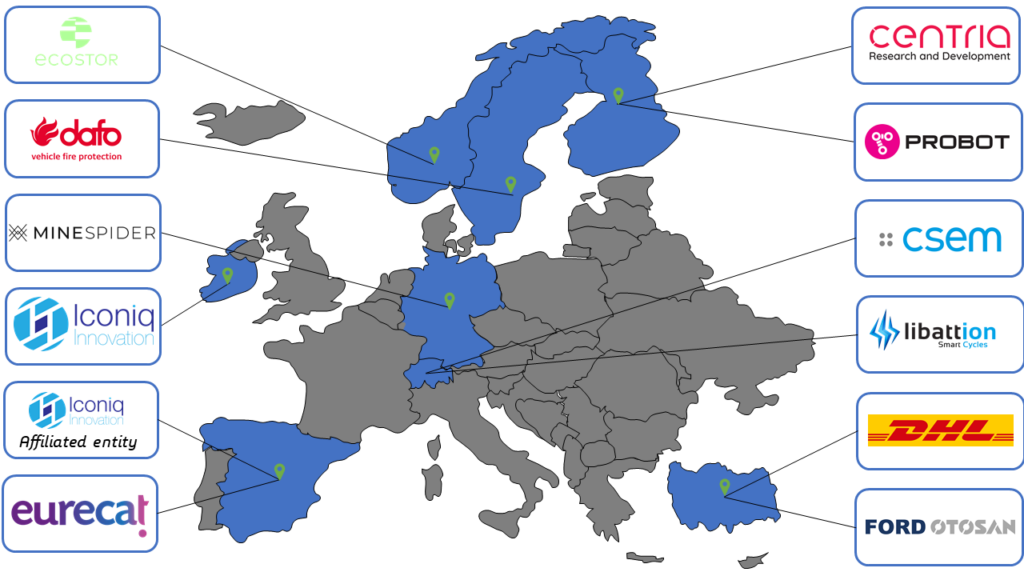
Kick-off meeting
The project kick-off meeting was in Helsinki on the 1st of June 2023; it was an excellent opportunity for participants to introduce themselves and meet the project personnel (Fig. 4). The EC Project Officer participated online to introduce himself and present standard guidelines of an EU Horizon project. After the day-long meeting, we had a short break before dinner at the Lappi restaurant in Central Helsinki. The dinner was an excellent opportunity for non-formal discussions on the project and personal interests.

Development environments
Building the infrastructure for the battery dismantling laboratory and the battery storage is ongoing. The batteries are stored inside a container located outside to ensure fire safety, and only one battery pack at a time is inside the dismantling laboratory. The robot station for dismantling is set up next to the production automation laboratory at Centria. The space is isolated from the main building, providing good ground for the robotized dismantling laboratory. The structure of the dismantling robot cell was designed and installed by the project group at Centria.
Applying permits for storing, handling, and sorting the batteries has been a time-consuming process. The legislation for battery dismantling is still incomplete, and the authorities need a clear set of rules. Therefore, practices vary between different regions, and authorities have differing battery storage and handling demands. At the time of writing this article, the permit process has advanced, and we now have official permits for storing and handling EV batteries until the project ends in 2026.
Hybrid electronic vehicle battery packs received from Ford Otosan in June are currently stored in the container. Instead of being used as spare parts these packs are used for research and development. The shipment consisted of two types of batteries: small hybrid battery and plug-in-hybrid EV battery. Both of the batteries are used to power various models of Ford Transit Van. The shipment was received in June and the battery types are presented in Fig. 5.
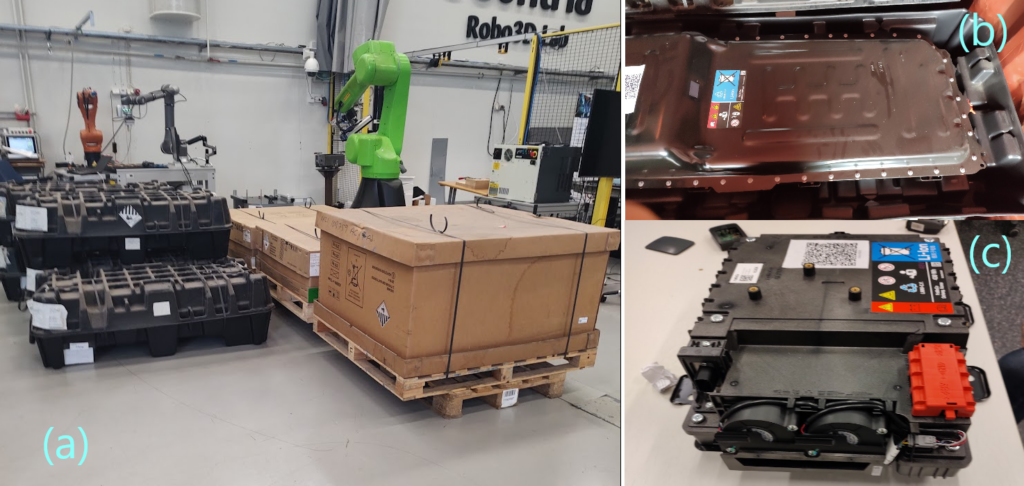
Simulation and 3D-modelling
Simulation of the process is essential to developing robotized dismantling and sorting EV batteries. Simulations enable planning for layout, tooling, and disassembly sequence. The layout solution for the dismantling cell was decided based on simulation results. The robot is installed on a linear track, hanging downward over the battery being dismantled. The robot is supported by a frame structure mounted on the floor. Fig 6. presents the robot cell physical installation and the corresponding view of the simulation.
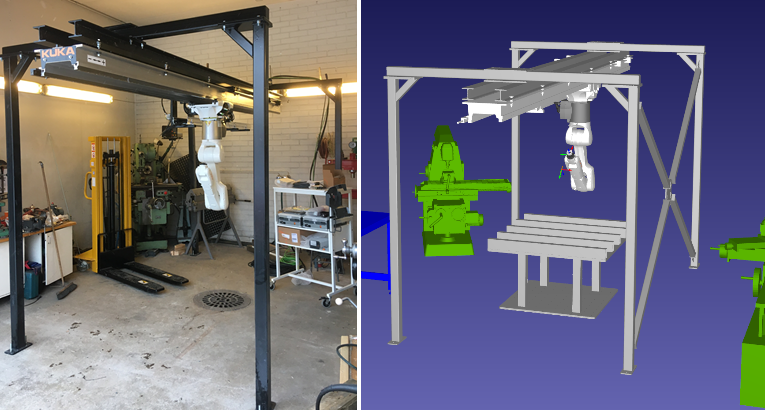
RoboDK (RoboDK Inc., Canada) simulation software is used at Centria to simulate the dismantling robot. RoboDK is one of the simulation software integrated into education, enabling fluent collaboration between students and RECIRCULATE project. Probot utilized KukaSIM (Kuka AG, Germany) simulation software to enable more profound engagement with the industry, as Probot’s responsibility is to demonstrate the dismantling and sorting solution in an industrially relevant environment.
The batteries received from Ford Otosan were disassembled to digitize all the parts to provide material for simulations and to define the tools required for disassembling the battery packs. As the idea is to dismantle the packs with all the parts intact, cutting or other destructive methods cannot be used. One of the main challenges will be in creating methods for detaching electrical wiring assembly connectors intact. In Fig. 7. Pekka Haapala is scanning the hybrid EV battery to create digitized models for simulation.
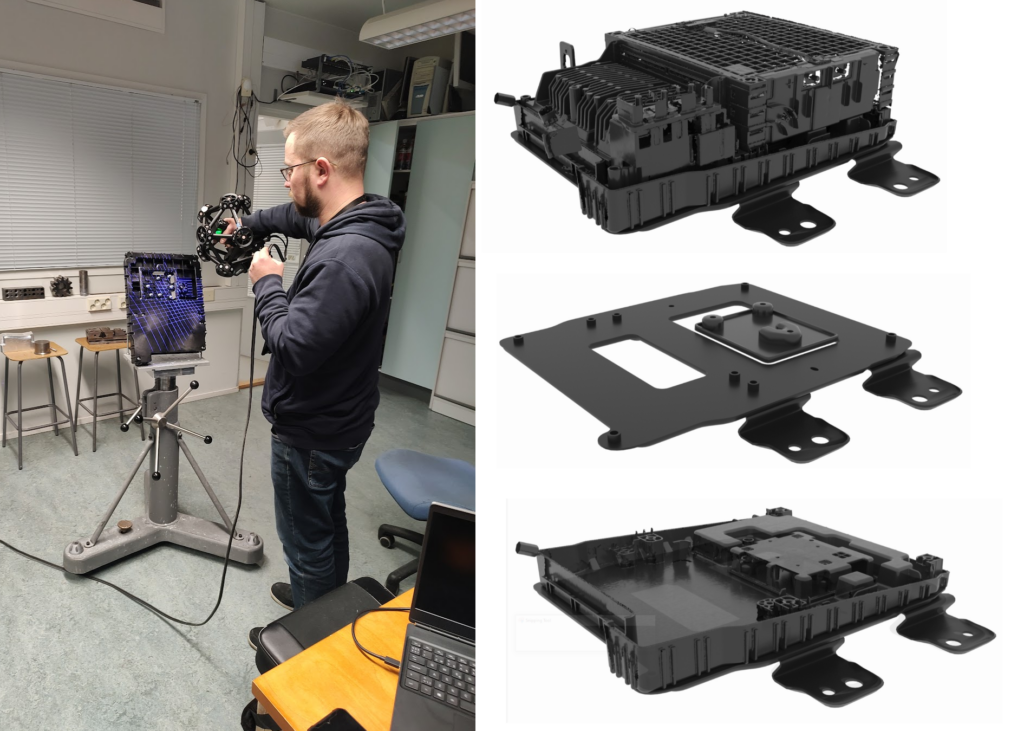
Observed challenges
The connectors have a locking tab, requiring simultaneous pressing and pulling action for removal (Fig. 8). Some of the connectors are physically small, and some connectors have a securing tab requiring removal before pressing the locking tab. The fine motoric pattern for detaching the connectors requires a variety of grippers to adapt different size connectors, machine vision to locate the connector tabs, and a force sensor to control the pressing and pulling actions during the process. Overcoming the challenge requires extensive planning, prototyping and testing.
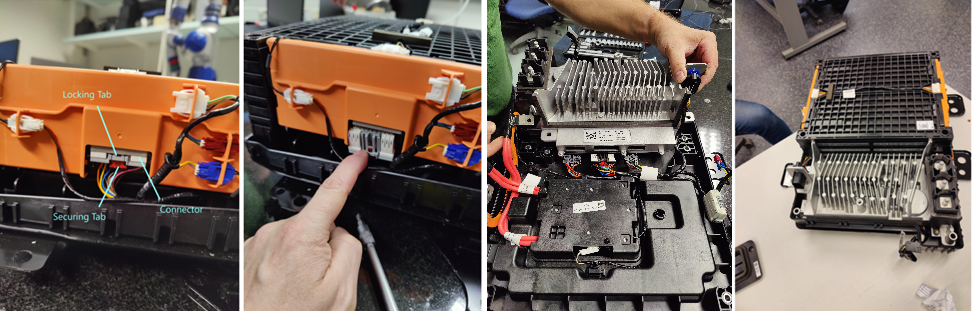
To ensure safety, it is important to define the condition of the battery prior to dismantling and monitoring the state of the battery pack during disassembly. Centria is developing sensor fusion technology to monitor the state of the battery during the dismantling process (Fig. 9). The environment for monitoring consists of thermal camera, hydrogen fluoride sensor, voltage meter and CAN-bus adapter. Thermal camera detects and indicates sudden rise in battery cells temperatures to isolate the short-circuited cells. The voltage meter registers short-circuit by monitoring sudden voltage dips and the hydrogen fluoride sensor detects chemical leaks from the battery cells. The CAN-bus is used to extract critical battery data during the dismantling process.
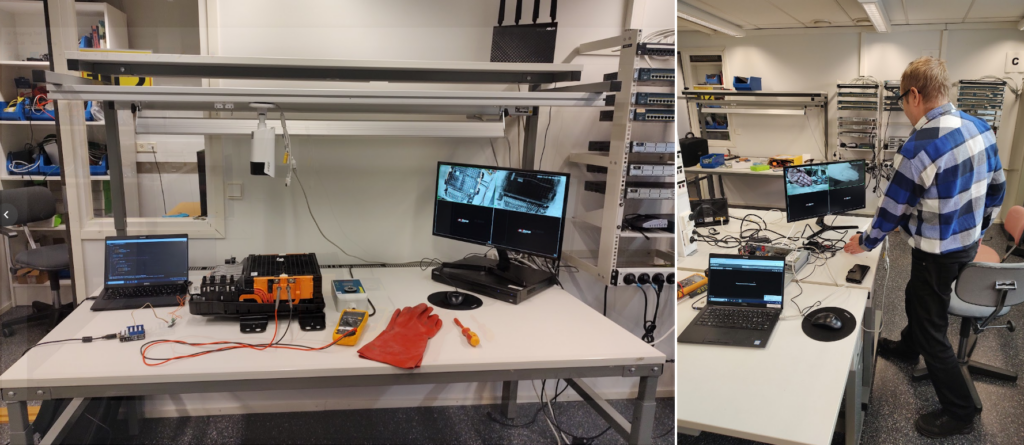
Conclusion
RECIRCULATE is addressing the current challenges in the European recycling sector by developing an advanced EV battery repurposing and recycling concept. Robotized dismantling, fast and reliable condition characterization, and safe logistics provide a solid base for the concept. Battery passport and virtual marketplace enable marketing concepts for the repurposed EV batteries as consumer and energy storage systems. Solutions developed will enable increased end-of-life battery repair, reuse, remanufacture and recycling, creating new circular business models while minimizing costs, time, energy, and environmental impact. Solutions for reusing and recycling the EV batteries are needed since the electrifying of logistics is ramping up. In addition to passenger vehicles, powertrains of commercial vehicles are electrified for sustainability and profitability. An electric truck and vans are presented in picture 10. The vans are manufactured by Ford Otosan and after servicing the logistics sector, batteries are reused and eventually recycled.
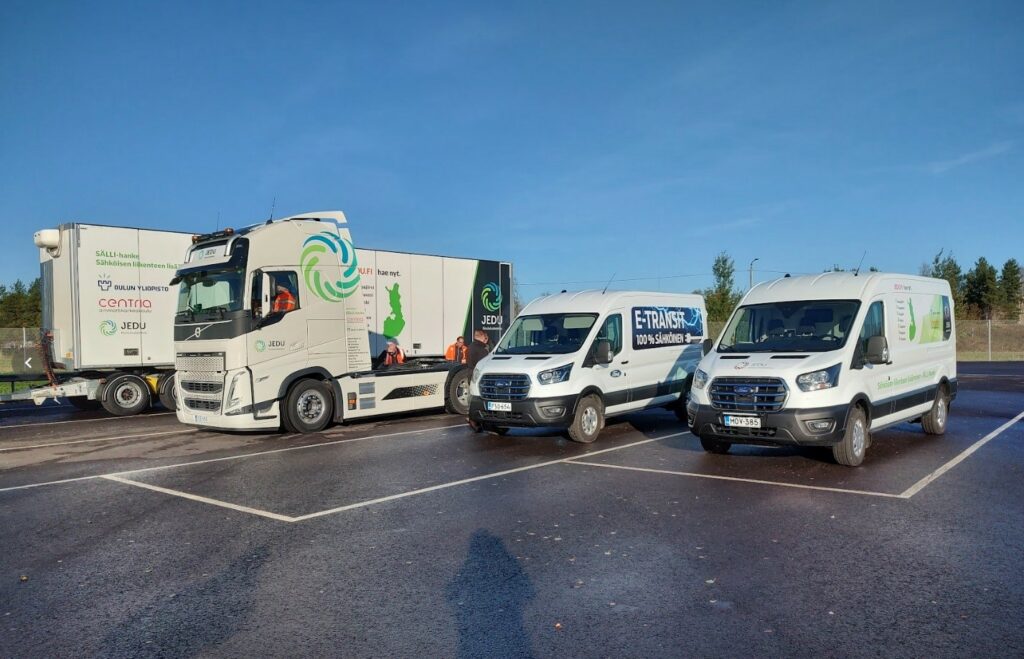
The methods and concepts developed in the project will supersede the current time-consuming, hazardous, and cost-ineffective manual dismantling and sorting of the EV batteries. In addition, the developed methods extend the lifecycle of batteries by repairing, reusing, and repurposing for second-life applications.
Intelligent logistics solutions combined with battery passports ensure the safe storage, transportation, and marketing of repurposed batteries. With a European consortium of world-leading organizations, RECIRCULATE has the potential to create a sustainable future for the battery circular economy, utilizing the aforementioned technologies.
Centria is gaining experience and merit in leading a European consortium and developing novel methods for robotized dismantling and sorting EV batteries during the project. Centria is the only university in the project and is the responsible partner for publishing project achievements in scientific journals, articles and conferences. Publishing articles about cutting-edge methods developed is our obligation, and we have already started working on publishing the results at full steam to meet the expectations set for us.
RECIRCULATE is funded by the European Union, grant agreement n° 101103972. Views and opinions expressed are however those of the author(s) only and do not necessarily reflect those of the European Union or [name of the granting authority]. Neither the European Union nor the granting authority can be held responsible for them.
Tomi Pitkäaho
R&D Manager
Centria University of Applied Sciences
tel. +358 40 485 8219
Athith Sagar
RDI Coordinator
Centria University of Applied Sciences
tel. +358 40 635 9442
Tero Kaarlela
Lecturer
Centria University of Applied Sciences
tel. +358 40 487 7513

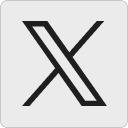

